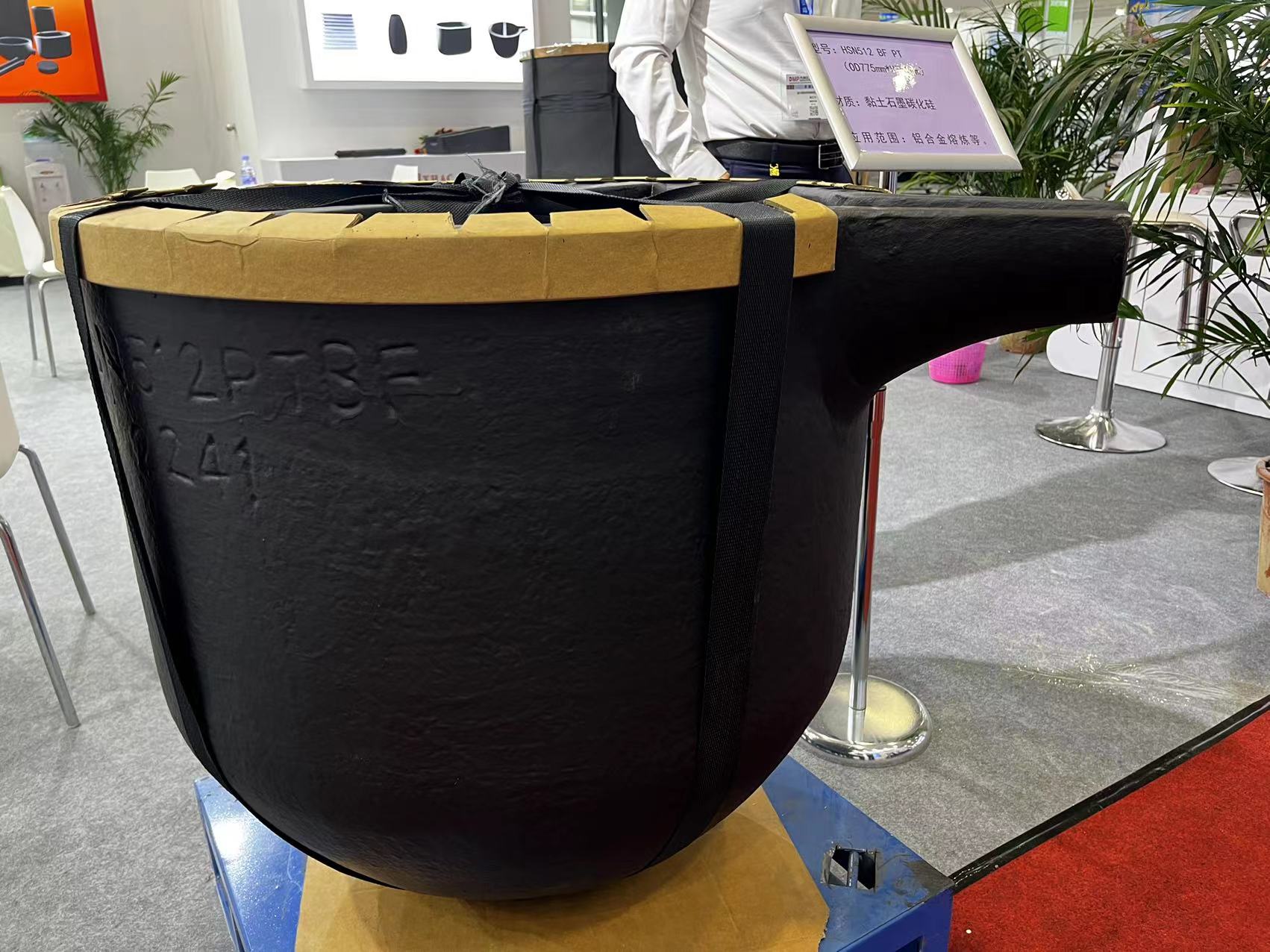
Valmistusmenetelmä, jolla on erittäin lujagrafiittipiilarbidi -upokasMetallin sulatus sisältää seuraavat vaiheet: 1) raaka -aineiden valmistus; 2) ensisijainen sekoitus; 3) materiaalin kuivaus; 4) murskaus ja seulonta; 5) toissijainen materiaalin valmistelu; 6) sekundaarinen sekoitus; 7) puristaminen ja muovaus; 8) leikkaaminen ja leikkaaminen; 9) kuivaus; 10) lasitus; 11) ensisijainen ampuminen; 12) kyllästys; 13) toissijainen ampuminen; 14) päällyste; 15) Valmiste. Tätä uutta kaavaa ja tuotantoprosessia käyttämällä upokas on voimakas korkean lämpötilan vastus ja korroosionkestävyys. Upokan keskimääräinen elinikä on 7-8 kuukautta tasaisella ja virheettömällä sisäisellä rakenteella, korkealla lujuudella, ohuilla seinillä ja hyvällä lämmönjohtavuudella. Lisäksi lasituskerros ja pinnoite pinnalla yhdessä useiden kuivaus- ja ampumisprosessien kanssa parantavat merkittävästi tuotteen korroosionkestävyyttä ja vähentävät energiankulutusta noin 30%: lla, korkealla lasitusasteella.
Tämä menetelmä käsittää ei-rautametallurgian valun kentän, etenkin valmistusmenetelmän, jolla on erittäin luja grafiittikarbidi-upokas metallin sulattamiseen.
[Taustatekniikka] Erityistä grafiittikarbidi-upotuksia käytetään pääasiassa ei-rautametallien valu- ja taontaprosesseissa, samoin kuin jalometallien palautumisessa ja puhdistamisessa sekä korkean lämpötilan ja korroosiokeskeisten tuotteiden tuotannossa, joita tarvitaan muovien, keramiikan, lasi-, sementtien ja kumi- ja lääketeollisuuden ja farekialousaineiden ja farekialousaineiden, kuten forekialousaineiden ja farekialousmiehen ja sementtien valmistustuotteidensa tuotantoon.
Nykyiset erityiset grafiittikarbidi -upokkaat formulaatiot ja tuotantoprosessit tuottavat tuotteita, joiden keskimääräinen elinikä on 55 päivää, mikä on liian lyhyt. Käyttö- ja tuotantokustannukset kasvavat edelleen, ja myös tuotettu jätteen määrä on suuri. Siksi uuden tyyppisen erityisgrafiittipidikarbidi -upokkaan ja sen tuotantoprosessin tutkiminen on kiireellinen ongelma, koska näillä upokkailla on merkittäviä sovelluksia erilaisilla teollisuuskemikaaleilla.
Edellä olevien ongelmien ratkaisemiseksi tarjotaan menetelmä erittäin lujan grafiittikarbidi-upokkaiden valmistelemiseksi metallin sulattamiseksi. Tämän menetelmän mukaisesti valmistetut tuotteet kestävät korkeita lämpötiloja ja korroosiota, niillä on pitkä käyttöikä ja saavuttaa energiansäästöjä, päästöjen vähentämistä, ympäristönsuojelua ja suurta jätteiden kierrätysnopeutta tuotannon aikana, maksimoimalla resurssien kierto ja hyödyntäminen.
Metallin sulattamisen erittäin lujuuden grafiittikarbidi-upokkaiden valmistusmenetelmä sisältää seuraavat vaiheet:
- Raaka -aineiden valmistus: Piharbidi, grafiitti, savi ja metallinen pii asetetaan vastaaviin ainesosien säiliöihin nosturilla, ja PLC Pneumaattiset venttiilit hallitsevat purkausta, ja ainakin kaksi punnitusanturia asetetaan kunkin ainesosan alareunan alaosaan. Punninnoituksen jälkeen materiaalit asetetaan sekoituskoneeseen automaattisen siirrettävän kärryn avulla. Piharbidin alkuperäinen lisäys on 50% sen kokonaismäärästä.
- Toissijainen sekoitus: Kun raaka -aineet on sekoitettu sekoituskoneessa, ne puretaan puskurisovelluksiin ja puskurisovelluksen materiaalit nostetaan sekoitussuppilaan ämpäri -hissillä sekundaarista sekoittamista varten. Raudan poistolaite asetetaan kauhan hissin purkausporttiin, ja veden lisäyslaite asetetaan sekoitussupperin yläpuolelle veden lisäämiseksi sekoittaen. Veden lisäysnopeus on 10 litraa/min.
- Materiaalin kuivaus: Märkä materiaali sekoittamisen jälkeen kuivataan kuivauslaitteessa lämpötilassa 120-150 ° C kosteuden poistamiseksi. Täydellisen kuivumisen jälkeen materiaali viedään luonnollisen jäähdytyksen vuoksi.
- Murskaus ja seulonta: Kuivattu rypistynyt materiaali menee murskaus- ja seulontalaitteisiin esimurhaa varten, sitten kulkee vastahyökkäysmurskaimen edelleen murskaamiseksi ja kulkee samanaikaisesti 60 mesh-seulontalaitteiden läpi. Yli 0,25 mm: n hiukkaset palautetaan kierrätykseen edelleen esikurjamista, murskaamista ja seulontaa varten, kun taas pienempiä kuin 0,25 mm: n hiukkasia lähetetään suppilolle.
- Toissijainen materiaalivalmistus: Vastuuvapauden materiaalit kuljetetaan takaisin eräkoneeseen toissijaista valmistelua varten. Loput 50% piikarbidista lisätään toissijaisen valmisteen aikana. Materiaalit toissijaisen valmistuksen jälkeen lähetetään sekoituskoneeseen sekoittamista varten.
- Toissijainen sekoitus: Toissijaisen sekoitusprosessin aikana sekoitussuppilaan lisätään erityinen liuos viskositeettiin erityisen liuoksen lisäämisen laitteen avulla, jolla on tietty painovoima. Erityinen liuos punnitaan punnittavalla ämpäri ja lisätään sekoitussuppilaan.
- Painaminen ja muovaus: Materiaalit sekundaarisen sekoituksen jälkeen lähetetään isostaattiselle puristuskoneen suppilolle. Lataamisen, tiivistymisen, imuroin ja puhdistuksen jälkeen muotissa materiaalit puristetaan isostaattisessa puristuskoneessa.
- Leikkaus ja trimmaus: Tähän sisältyy korkeuden leikkaaminen ja upottavien haurien leikkaaminen. Leikkaus tehdään leikkauslaitteella upokkaan leikkaamiseksi vaaditulle korkeudelle, ja leikkauksen jälkeen leikkurin jälkeen.
- Kuivaus: Upokas, kun se on leikattu ja leikattu vaiheessa (8), lähetetään kuivausuuniin kuivumista varten, kun kuivauslämpötila on 120-150 ° C. Kuivauksen jälkeen sitä pidetään lämpimänä 1-2 tuntia. Kuivausuuni on varustettu ilmakanavan säätöjärjestelmällä, joka koostuu useista säädettävistä alumiinilevyistä. Nämä säädettävät alumiinilevyt on järjestetty kuivausuunin kahdelle sisäpuolelle ilmakanavalla jokaisen kahden alumiinilevyn välillä. Jokaisen kahden alumiinilevyn välinen rako säädetään ilmakanavan säätelemiseksi.
- Lasitus: Lasite valmistetaan sekoittamalla lasitusmateriaaleja veteen, mukaan lukien bentoniitti, tulenkestävä savi, lasijauhe, maasäilyjauhe ja natriumkarboksimetyyliselluloosa. Lasite levitetään manuaalisesti siveltimellä lasituksen aikana.
- Ensisijainen ampuminen: Upokas levitetyllä lasilla amputaan kerran uunissa 28-30 tunnin ajan. Ammustehokkuuden parantamiseksi labyrintin uunikerroksella, jolla on tiivistysvaikutus ja ilman tukkeutuminen uunin pohjalle. Uunakerroksessa on pohjasuoja tiivistystautoa, ja tiivistimen yläpuolella on eristystiilikerros, joka muodostaa labyrinttiuunin sängyn.
- Kytkentä: ampunut upokas asetetaan kyllästyssäiliöön tyhjiö- ja paineen impregnointia varten. Kytkentäratkaisu kuljetetaan kyllästyssäiliöön suljetun putkilinjan läpi, ja kyllästysaika on 45-60 minuuttia.
- Toissijainen ampuminen: Kilmittynyt upokas asetetaan uuniin sekundaarisen ampumisen vuoksi 2 tunnin ajan.
- Pinnoite: Upokas sekundaarisen ampumisen jälkeen on päällystetty vesipohjaisella akryylihartsimaalilla pinnalla.
- Valmiste: Kun pinnoite on valmis, pinta on kuivattu ja kuivumisen jälkeen upokas pakataan ja varastoidaan.
Viestin aika: Mar-20-2024